Research Activities
Molecular Dynamics Simulations of Grain Boundary Migration and Grain Growth
We have determined the velocity and curvature of approximately 12000 grain boundaries from molecular dynamics simulations of the annealing of randomly textured nanosized polycrystalline Al. The grain boundary kinetics was studied at different scales and compared with theoretical predictions. At the grain level, that is, attributes averaged over all grain boundaries of a grain, the kinetics behavior showed a linear correlation of curvature and velocity. When studying grain-boundary-level behavior (i.e., attributes of individual grain boundaries are considered), we found a clear correlation between the sign of the grain boundary curvature and the direction of migration. Nevertheless, considering all the grain boundaries, the correlation coefficient between the magnitude of velocity and curvature was found to be low although a strong linear correlation was observed for a subset of high angle, long-lived, initially large grain boundaries with uniform curvature distribution and unchanged 5 crystallographic degrees of freedom with time.
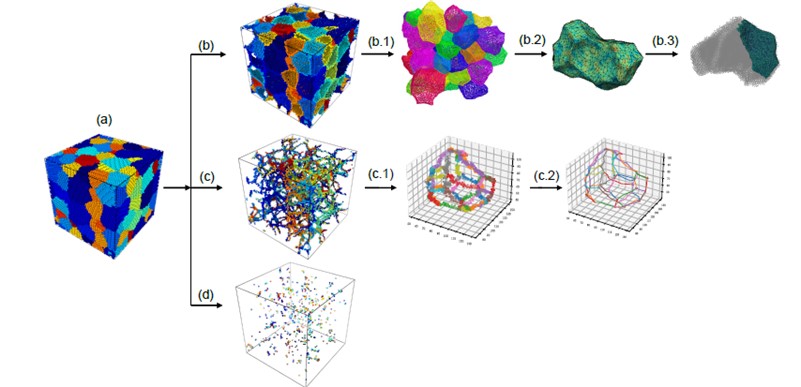
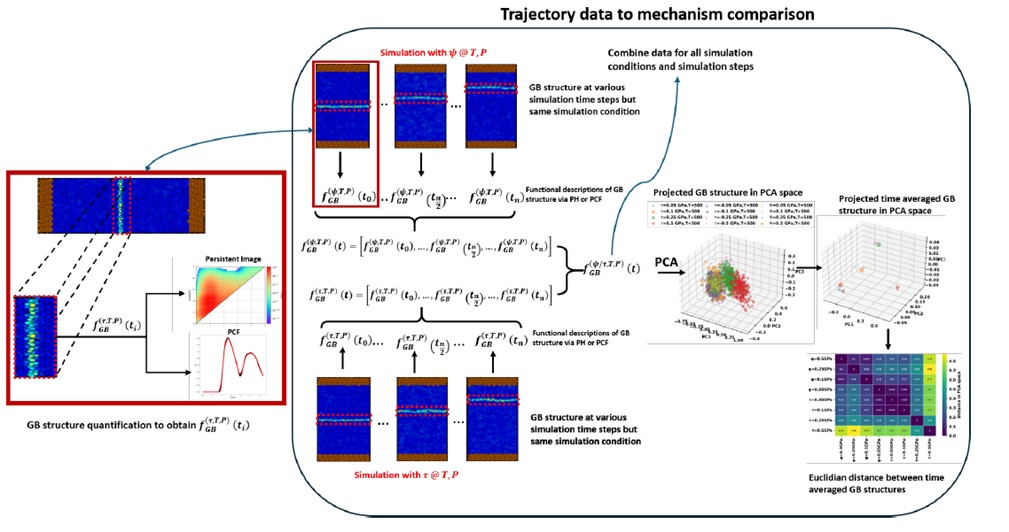
A physics-driven modeling on the process-structure-property linkage in additive manufacturing
Laser Powder Bed Fusion (LPBF) process holds significant potential in material design and offers the ability to engineer locally microstructures. However, alloys produced via LPBF often exhibit distinct microstructure features compared to traditional casting methods, primarily attributed to the directional temperature gradient and rapid cooling rate inherent in the LPBF process. This heterogeneity in microstructure further leads to the difference in mechanical properties. We have developed a physics-driven framework on process-structure-property relationships for LPBFed that has been tested in a scandium-modified alloy. A Cellular Automaton (CA) model is implemented for the investigation of the microstructure evolution and a physics-based crystal plasticity (CP) model is used for predicting the mechanical properties. For modelling the precipitation of second phases during the melt, a Classical Nucleation and Growth (CNGT) model has been coupled with the CA model to determine the volume percentage and average size of the major Al3Sc precipitates during printing. This microstructure, compared with characterization, is validated and applied as a representative volume element (RVE) in CP model simulations. For validation, the simulation results are compared with experimental findings.
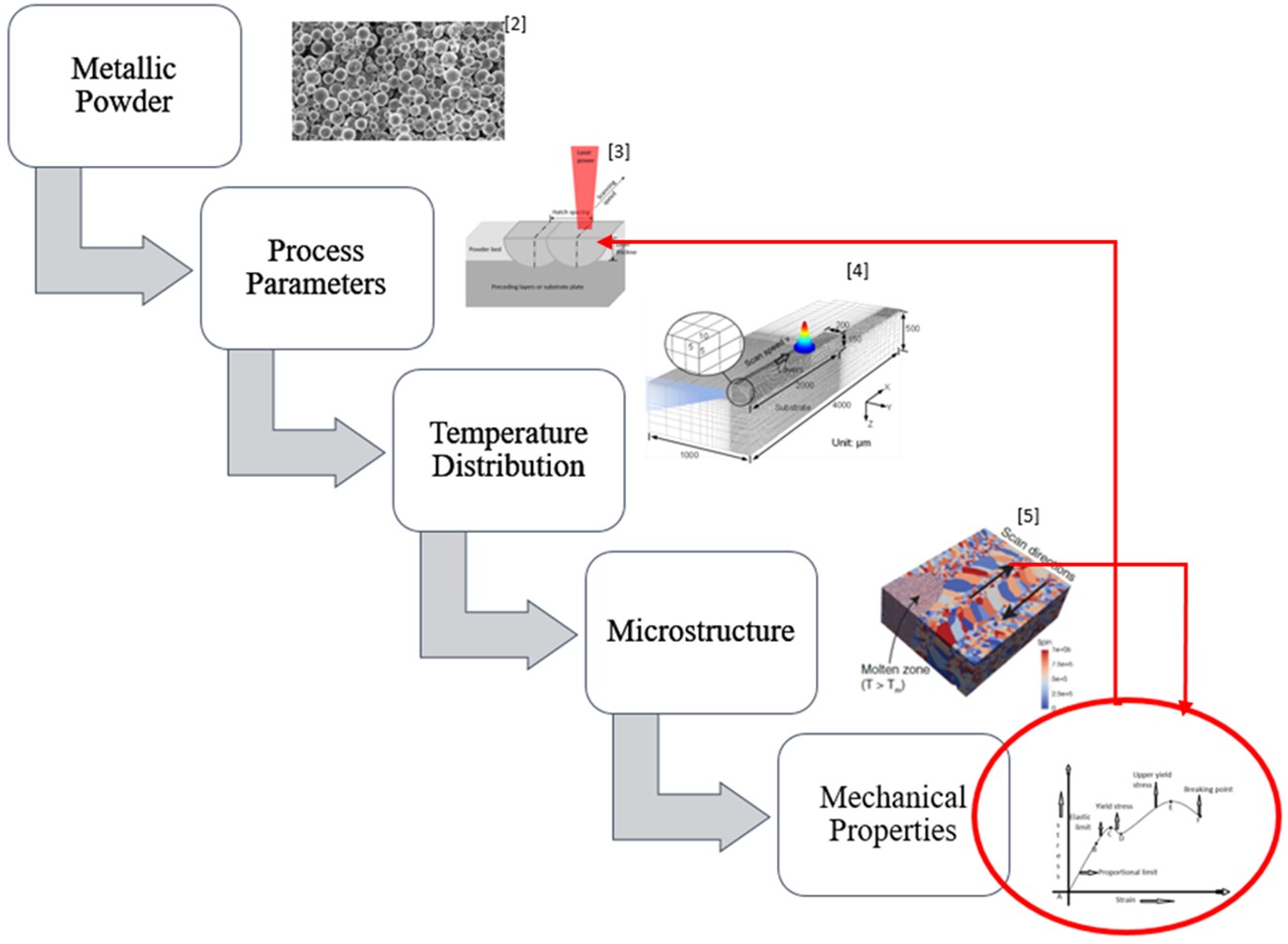
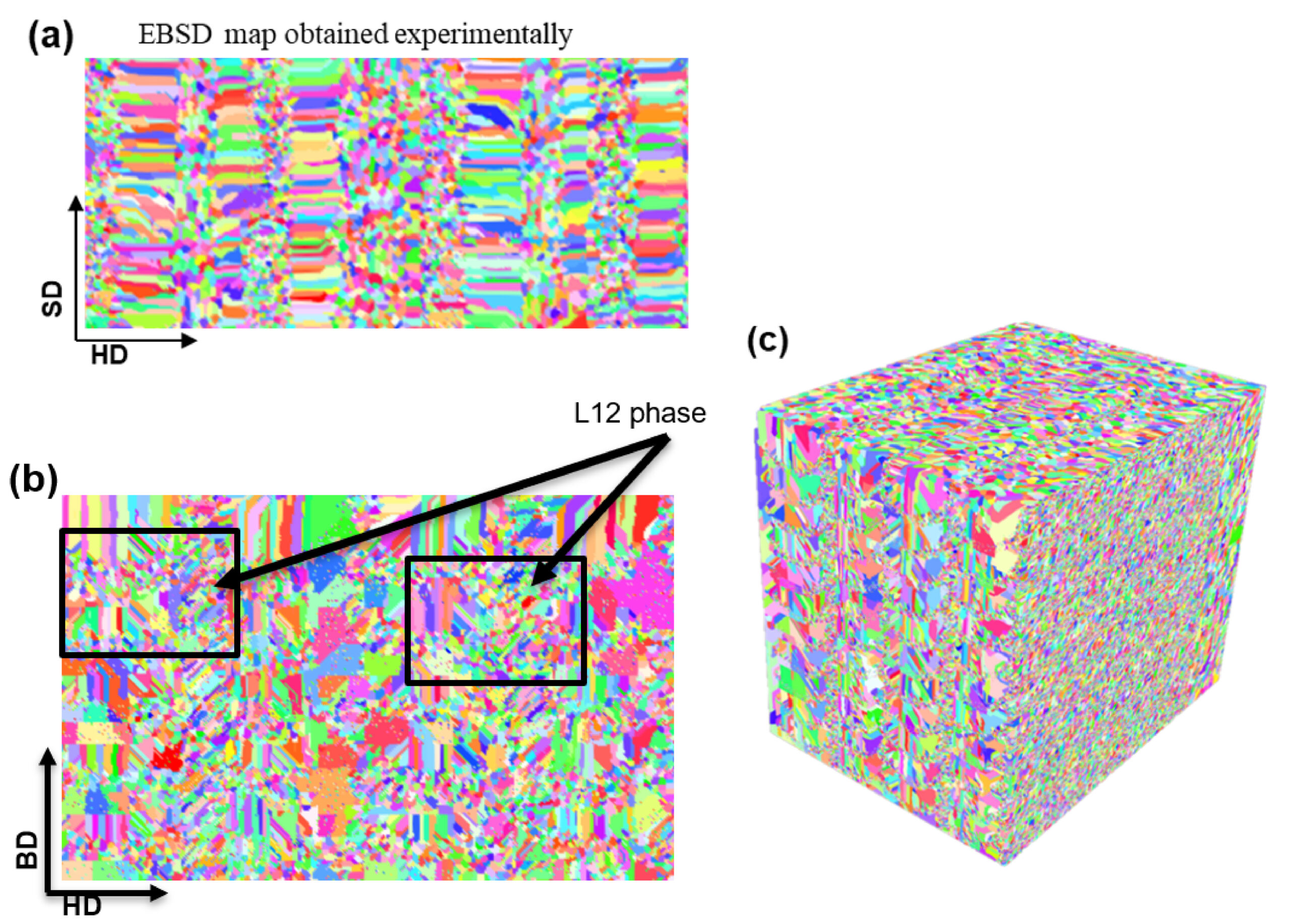